Disc coupling is a flexible shaft connector that transmits torque tangentially between driving and driven bolts positioned on a shared bolt circle. This torque transmission occurs through stainless-steel discs, meticulously arranged in a pack. Designed for high-performance motion control applications, disc couplings can accommodate rotational speeds up to an impressive 10,000 rpm.
The Working Principle of Disc Coupling
Disc coupling is a flexible shaft connector that transmits torque tangentially between driving and driven bolts positioned on a shared bolt circle. This torque transmission occurs through stainless-steel discs, meticulously arranged in a pack. Designed for high-performance motion control applications, disc couplings can accommodate rotational speeds up to an impressive 10,000 rpm.
Varieties of Disc Coupling
Disc coupling is a flexible shaft connector that transmits torque tangentially between driving and driven bolts positioned on a shared bolt circle. This torque transmission occurs through stainless-steel discs, meticulously arranged in a pack. Designed for high-performance motion control applications, disc couplings can accommodate rotational speeds up to an impressive 10,000 rpm.
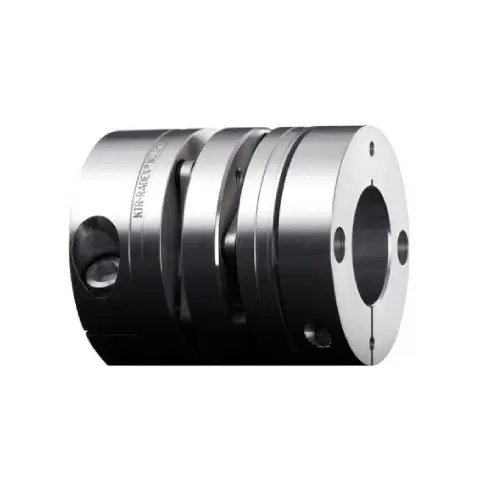
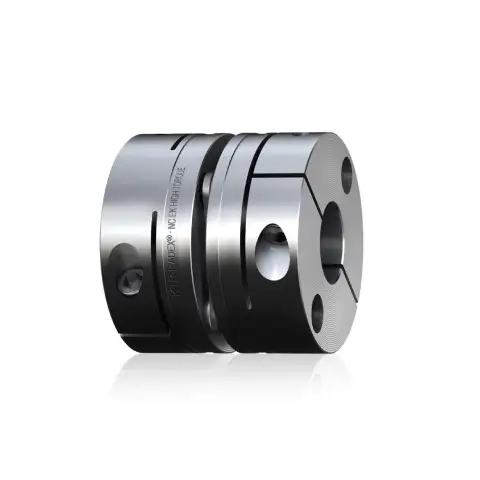
Disc couplings are available in two primary styles: single-disc and double-disc couplings.
Single-disc couplings feature two hubs, often crafted from aluminium or stainless steel, and a singular, flat, stainless steel disc spring. In contrast, double-disc couplings also comprise two hubs but include an additional spacer positioned between two-disc springs. This spacer can be constructed from the same material as the hubs or from electrically isolating materials.
A single-disc pack can accommodate angular and axial misalignment, while two-disc packs are necessary to address parallel misalignment.
Functional Attributes of Disc Coupling
Transmit torque between machinery components.
Accommodate various misalignments while minimizing reactive forces on the equipment.
Dampen harmful peak torques and torsional vibrations.
Provide overload protection to prevent the transmission of damaging loads.
Prevent electrical shorting between equipment by incorporating electrical insulation.
Offer live torque and power readings with less than 1% error.
Applications of Disc Coupling:
Disc couplings find extensive use in large industrial machines such as pumps, blowers, compressors, and mixers. They are particularly suited for medium- and heavy-duty applications where balance is crucial. Additionally, they are effective in smaller motion-control installations.
Advantages of Disc Coupling
Disc coupling is a flexible shaft connector that transmits torque tangentially between driving and driven bolts positioned on a shared bolt circle. This torque transmission occurs through stainless-steel discs, meticulously arranged in a pack. Designed for high-performance motion control applications, disc couplings can accommodate rotational speeds up to an impressive 10,000 rpm.
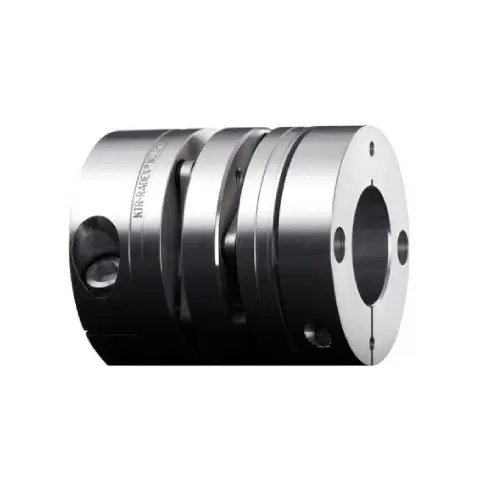
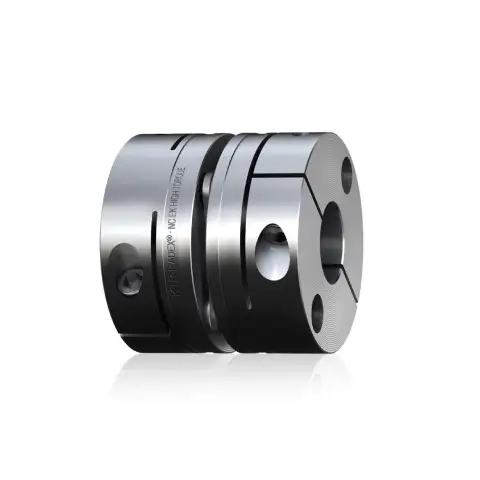
Eliminate the need for lubrication and maintenance.
Allow for inspection without disassembly.
Enable inspection of disc packs with a strobe light during operation.
Simplify the assessment of equipment misalignment.
Provide torsional rigidity without backlash.
Feature no wearing parts.
Utilize high-strength, flexible stainless-steel discs.
Resist harsh environmental conditions.
Offer long service life when properly sized and aligned.
Deliver high power density (higher torque for a given outside diameter).
Handle high shock loads to a certain degree.
Compensate for angular and parallel misalignment between shafts.
Reduce maintenance time and costs.
Disc couplings are often employed in power transmission applications, especially where motors exceed 200 HP and the use of journal bearings is common.